AI at the Process Level: How AI and Cyber-Physical Systems are shaping Manufacturing Excellence
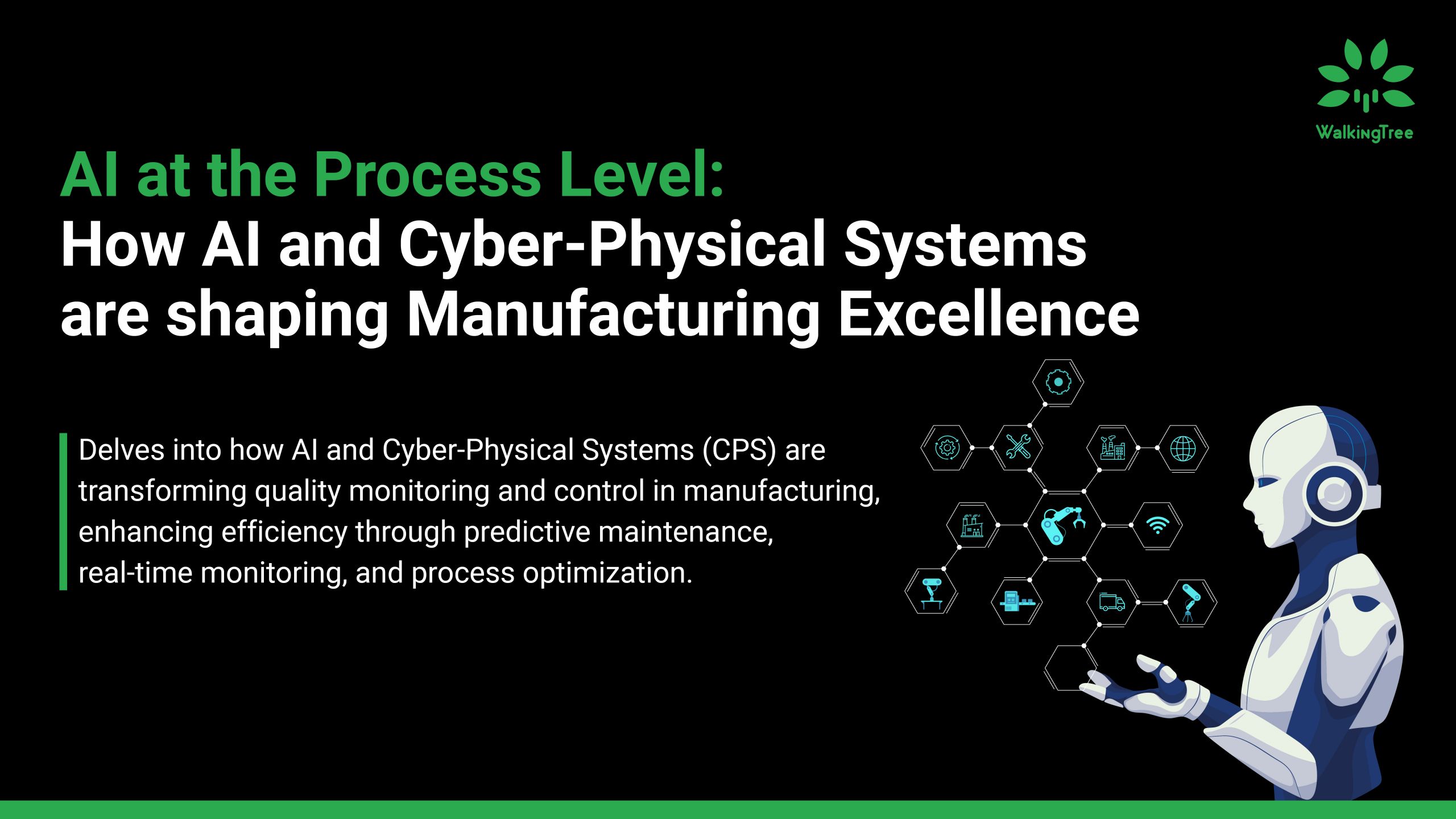
Artificial Intelligence (AI) and Cyber-Physical Systems (CPS) are becoming disruptive technologies in a time where digitalization is transforming industrial and manufacturing processes, especially in quality control and monitoring. Applying AI to processes has shown to be a crucial strategy for companies that prioritize operational efficiency and innovation. Cyber-physical systems (CPS) and AI-powered quality monitoring are two of the key components that allow manufacturing organizations to make the shift to smart factories. These technologies help companies create better-quality products, run their operations more effectively, and experience less downtime.
AI at the process level provides real-time data analysis, proactive interventions, and predictive insights to improve decision-making. This capability extends to process optimization, defect prediction, and autonomous control to guarantee product compliance with industry requirements in quality monitoring. In this blog, we’ll examine case studies that highlight the significance of AI and CPS in manufacturing excellence as well as go deeper into how they contribute to quality control and monitoring.
|The Advancement of AI-Powered Quality Monitoring
Human interaction and periodic inspections have always been the mainstays of quality monitoring in manufacturing. However, quality control procedures have changed as a result of Industry 4.0, becoming more proactive, dynamic, and integrated with automation powered by AI. The manufacturing quality can be tracked, analyzed, and controlled in real-time by manufacturers thanks to AI-based quality monitoring systems. This means that even minor deviations from standards may be handled before they become more serious issues.
Key advancements include:
- Real-time Anomaly Detection: Micro-level defect detection in real-time is possible with artificial intelligence (AI) systems that are outfitted with computer vision, pattern recognition, and predictive analytics. This makes it possible to make adjustments right away, cutting down on waste and avoiding the sale of faulty goods.
- Predictive Quality Analytics: AI-powered predictive analytics forecasts when a machine or process may stray from acceptable standards by analyzing past data. Higher operational efficiency results from ensuring that recalibration or preventative maintenance is done before faults arise.
- Process Optimization: AI can analyze large volumes of production data to identify patterns that suggest inefficiencies. By recommending process adjustments, AI can ensure optimal quality control without human intervention.
These advancements signify a shift from reactive quality control measures to proactive and autonomous quality assurance frameworks.
|Cyber-Physical Systems (CPS) and their Function in Quality Monitoring
The integration of computational algorithms with physical processes, or cyber-physical systems (CPS), enables real-time communication between computing systems and machinery. The foundation of intelligent automation and intelligent production in manufacturing is provided by CPS. Real-time process modifications and continuous quality monitoring are made possible by CPS’s ability to facilitate seamless communication between machines, sensors, and software.
Some key benefits of CPS in quality control include:
- Automated Monitoring: CPS makes sure that all production process steps are tracked and that any deviations from the target quality standards are automatically reported. This guarantees a more dependable and consistent quality production while lowering the dependency on human operators.
- Self-Optimizing Systems: AI-equipped devices can use CPS to automatically modify their activities in response to real-time sensor feedback. This self-optimization capacity reduces mistakes and raises manufacturing process accuracy.
- Data-Driven Decision Making: CPS gathers and examines information from the whole manufacturing ecosystem to give decision-makers useful information they can use to modify the production line and uphold high standards of quality.
|AI in Quality Control: Practical Applications
AI has found diverse applications in quality control across various industries. Here are some specific examples where AI-driven systems have significantly improved quality monitoring and control in manufacturing:
1. Automated Visual Inspection
Automated visual inspection systems driven by computer vision and machine learning algorithms are used in the electronics and automotive industries to find abnormalities, alignment problems, and surface flaws in products. These algorithms offer higher detection accuracy, can work around the clock, and function faster than human inspectors—especially for small flaws that are challenging to find manually.
Manufacturers of automobiles, for instance, utilize AI to check component assembly alignment, paint quality, and weld integrity. Because the AI models are trained on large datasets of both defective and defect-free products, they can instantly identify even the smallest abnormalities.
2. Predictive Maintenance in Quality Assurance
AI-powered predictive maintenance is essential to quality control since it can predict when a machine might break and result in flaws in the final product. For example, a machine can be serviced or calibrated before it produces defective parts if it is anticipated that it would diverge from its typical working circumstances. This strategy guarantees that only items that satisfy the highest quality standards are delivered and reduces downtime.
With the use of digital twin technology, WalkingTree’s predictive maintenance solutions simulate and forecast equipment behavior, enabling businesses to plan maintenance.
3. Real-Time Dashboarding for Quality Metrics
Manufacturers can keep a close eye on Key Performance Indicators (KPIs) connected to product quality thanks to AI-powered real-time dashboards. These dashboards give users immediate access to production quality data, which makes it simple to see patterns, locate bottlenecks, and address quality concerns as soon as they appear. Real-time dashboards, equipped with personalized alerts and automatic suggestions, serve as the central hub for quality assurance in contemporary production.
In one of WalkingTree’s projects, real-time dashboarding allowed a renewable energy firm to monitor thousands of operational signals from their equipment every two seconds. This system not only improved the firm’s ability to maintain quality but also enhanced operational efficiency.
|Case Studies: AI and CPS in Action
Case Study 1: Electronics Manufacturing with Automated Inspection
An AI-powered automated visual inspection system was put in place by an electronics manufacturer to raise the caliber of its printed circuit boards (PCBs). The AI algorithm scanned high-resolution photos of the boards, revealing faults that were previously undetected by human inspectors. The technology greatly increased product reliability by achieving greater accuracy and a 25% reduction in failure rate through the integration of computer vision and machine learning.
This case highlights the cost savings from lower rework and customer returns, as well as the productivity advantages possible from AI-powered automation in quality monitoring.
Case Study 2: Automotive Industry – Predictive Maintenance for Quality Control
To deploy a predictive maintenance system throughout its assembly lines, an automotive manufacturer teamed up with WalkingTree. The technology may anticipate equipment breakdowns before they happen by gathering data from IoT sensors integrated into machines and supplying it to AI algorithms. This strategy prevented machine problems that would have resulted in faulty parts by enabling the business to carry out maintenance at the best periods.
The manufacturer’s unplanned downtime was reduced by 40% and the overall quality of the product was enhanced by the integration of CPS with AI analytics.
Case Study 3: Food Processing – Ensuring Quality with AI-Driven Insights
Ensuring the safety and quality of products is crucial in the food industry. A food manufacturing company monitored real-time data from its production lines using AI-based quality analytics. The AI system made sure that every product complied with strict quality and safety criteria by evaluating temperature, humidity, and contamination threats. Additionally, the system offered suggestions for modifying processing parameters to prevent variations that would jeopardize quality.
This strategy strengthened the company’s brand recognition for producing high-quality goods while also improving compliance with food safety laws.
More developments in quality control using AI and CPS are anticipated in the future because of inventions like cobots—collaborative robots that work together—and increasingly complex AI-driven decision systems. Manufacturing businesses will be able to run at maximum efficiency and with no faults thanks to these technologies.
AI will keep developing and provide more insightful predictions, while CPS will improve the automation and flexibility of quality control procedures in real time. Consequently, enterprises that use these technologies will maintain a competitive edge by consistently and precisely producing outstanding products.
At WalkingTree, our expertise lies in assisting companies in deploying AI-powered solutions for process optimization and quality assurance. We guarantee that we will provide customized solutions that address your particular operating demands thanks to our broad experience in artificial intelligence, predictive analytics, CPS, and industrial automation. Our staff is here to support your digital transformation journey, no matter what your goals are—improving efficiency, cutting expenses, or improving product quality.
Contact WalkingTree today to learn more about how our AI and CPS solutions can revolutionize your quality control processes and drive measurable results. Visit our website for more information.