AI & Digital Twins: Smart Process Modeling for Manufacturing
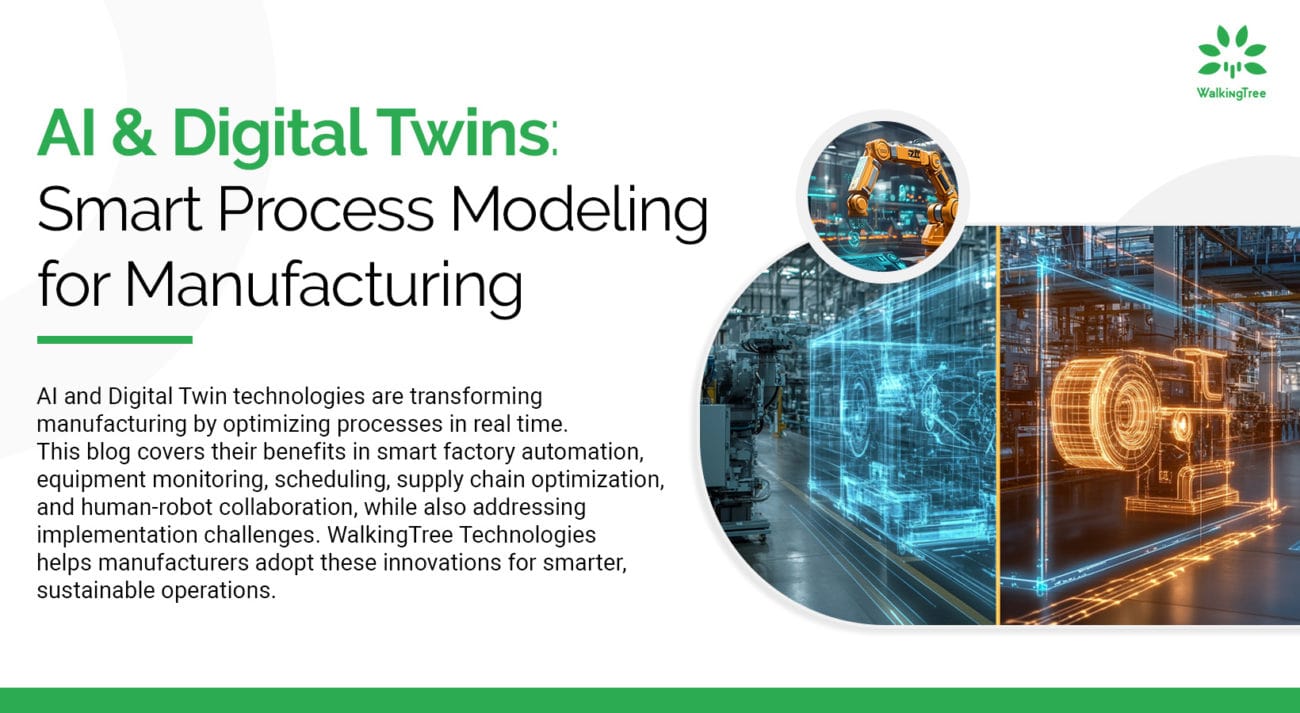
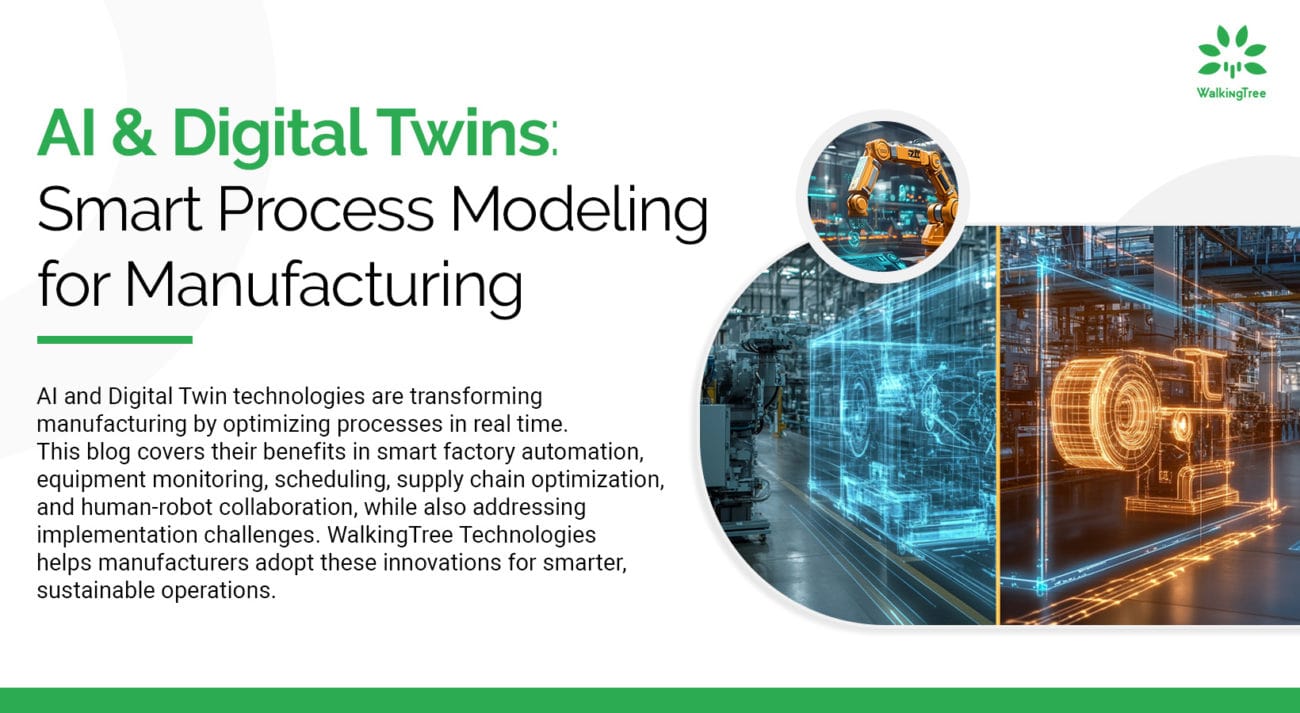
The manufacturing industry is undergoing a paradigm shift as AI-driven Digital Twins replace traditional process optimization methods. These intelligent virtual models, powered by Industry 4.0 technologies, allow manufacturers to simulate, predict, and optimize operations in real time. This leads to increased efficiency, cost reduction, and improved product quality. AI integration with Digital Twin technology enhances automation, operational intelligence, and predictive insights—fundamentally transforming manufacturing.
| The Growing Need for AI-Driven Digital Twins in Manufacturing
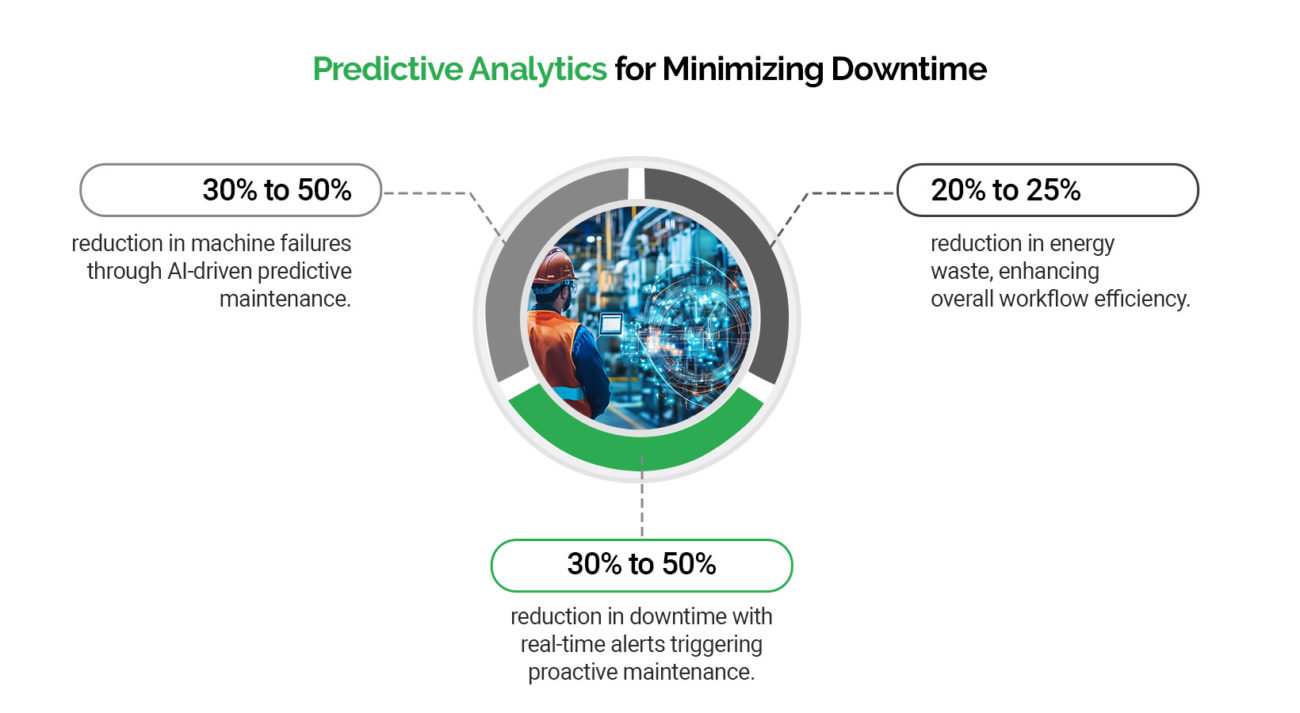
Industry reports highlight the increasing adoption and impact of AI-driven Digital Twins:
- Reduction in maintenance costs through predictive analytics: Predictive maintenance can reduce maintenance costs by 18% to 25%. mckinsey.com
- Decrease in operational downtime by preempting system failures: Predictive maintenance typically reduces machine downtime by 30% to 50%. mckinsey.com
- Increase in production efficiency through real-time process optimization: Implementing advanced scheduling algorithms into a plant digital twin can result in boosted throughput.
Why Manufacturers Must Adopt AI-Driven Digital Twins
Manufacturers must embrace AI-driven Digital Twins to:
- Enhance operational efficiency with real-time production insights.
- Enable predictive maintenance, reducing unexpected failures and costly downtimes.
- Simulate real-world scenarios for better supply chain agility and production planning.
- Ensure sustainable, energy-efficient production by lowering carbon footprints and material waste.
| Understanding Digital Twins & Smart Process Modeling
What is a Digital Twin?
A Digital Twin is a virtual replica of a physical object, system, or process that updates dynamically using real-time sensor data, AI, ML, and IoT. These models continuously learn from live data enabling businesses to simulate production conditions, detect anomalies, and implement proactive strategies before deploying changes in the actual environment.
Key Components of a Digital Twin:
- Physical Object or Process– Manufacturing equipment, production lines, or supply chain systems.
- Data Sensors & IoT– Real-time tracking of temperature, pressure, machine performance, and environmental factors.
- AI & Machine Learning Models– Predictive analytics for forecasting failures and optimizing workflows.
- Cloud & Edge Computing– Processing and storing vast amounts of sensor data for rapid decision-making.
- User Interface & Digital Dashboards– Real-time monitoring, reporting, and analytics for decision-makers.
| The Role of Smart Process Modeling
Smart Process Modeling involves the digital recreation of manufacturing workflows, enabling businesses to test, analyze, and refine operations in a virtual environment before implementation.
Key Advantages of Smart Process Modeling with Digital Twins:
- Predictive Failure Detection – AI-driven digital twins identify potential breakdowns before they happen, reducing unplanned downtime and saving operational costs.
- Process Optimization – By running simulations, businesses can test various manufacturing strategies, improving throughput and efficiency.
- Resource Utilization – Smart modeling ensures that materials, manpower, and energy resources are optimally allocated, reducing waste and improving sustainability.
- Real-time Scenario Planning – Digital twins can test “what-if” scenarios for supply chain disruptions, machine performance variations, or sudden demand surges, allowing manufacturers to make data-driven decisions proactively.
- Enhanced Product Lifecycle Management – Digital twins help companies track a product’s entire lifecycle, ensuring consistent quality and compliance with industry standards.
| AI’s Role in Digital Twins
AI enhances Digital Twin technology by adding adaptability, self-learning, and autonomous decision-making. Traditional Digital Twins relied on historical data and predefined rules, whereas AI-driven Digital Twins proactively learn from live data and make real-time adjustments.
How AI Enhances Digital Twins:
- Predictive Maintenance: AI-driven digital twins analyze real-time machine data to anticipate wear and tear, enabling condition-based maintenance instead of scheduled downtime.
- Autonomous Process Control: AI algorithms allow digital twins to self-optimize production lines, making intelligent decisions on speed, resource allocation, and workflow adjustments.
- Anomaly Detection & Quality Control: AI-powered pattern recognition detects defects, deviations, or inefficiencies in manufacturing processes, ensuring product consistency.
- Supply Chain Optimization: AI-driven digital twins integrate with real-time supply chain data to optimize logistics, warehouse management, and inventory control.
- Energy Efficiency & Sustainability: AI models within digital twins help reduce energy consumption, enhancing sustainability by predicting optimal energy usage patterns.
| Key Use Cases & Applications in Manufacturing
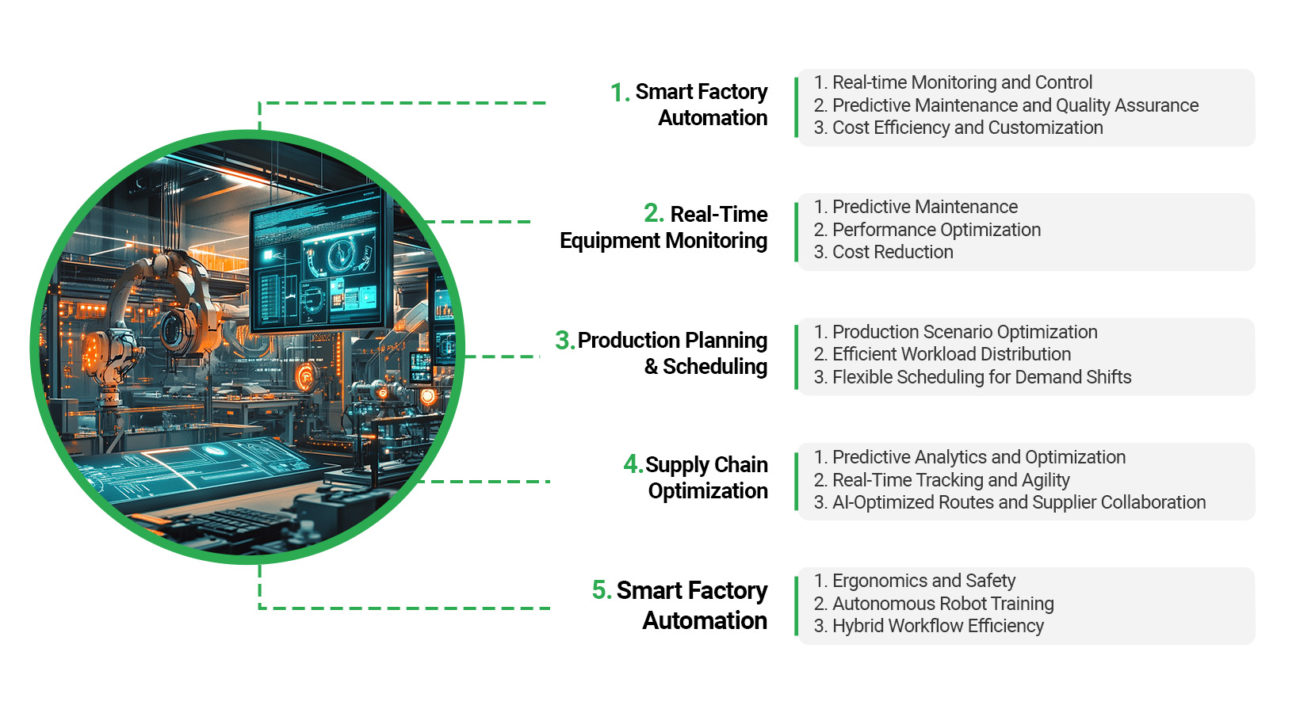
AI-powered Digital Twins and Smart Process Modeling are revolutionizing manufacturing by optimizing production efficiency, reducing downtime, and enhancing real-time decision-making. Below are key applications that demonstrate how these technologies are transforming industrial operations.
1. Smart Factory Automation
Digital twins, powered by AI, are at the core of smart factory automation, enabling manufacturers to simulate, control, and optimize production processes.
How It Works:
- Digital twins create a real-time virtual model of the entire factory floor, mirroring physical operations.
- AI continuously analyzes sensor data to automate machine settings and fine-tune workflows.
- Digital twins help minimize human intervention by enabling self-adjusting production lines.
Key Benefits:
✅ Enhanced production efficiency through automation and real-time decision-making.
✅ Reduced human error by using AI-powered real-time monitoring.
✅ Increased scalability, as digital twins adapt to changing production demands.
2. Real-Time Equipment Monitoring
AI-driven digital twins provide real-time insights into machine health, allowing manufacturers to track performance and detect failures before they occur.
How It Works:
- Sensors collect data on temperature, vibration, pressure, and efficiency.
- AI analyzes historical and live data to predict failures and optimize performance.
- Engineers receive real-time alerts and recommendations for maintenance actions.
Key Benefits:
✅ Predictive maintenance reduces downtime and extends equipment lifespan.
✅ Prevents unexpected failures, improving overall equipment efficiency (OEE).
✅ Reduces maintenance costs by up to 30%.
3. Production Planning & Scheduling
AI-powered simulations help manufacturers optimize production scheduling, balance workloads, and minimize bottlenecks.
How It Works:
- AI-driven digital twins simulate different production scenarios, analyzing efficiency, cost, and output.
- Helps manufacturers determine optimal machine utilization and workforce allocation.
- Allows for adaptive scheduling to handle unexpected demand spikes or disruptions.
Key Benefits:
✅ Reduces unplanned downtime and improves production agility.
✅ Enhances throughput by efficiently managing resources.
✅ Supports data-driven decision-making to optimize production lines.
4. Supply Chain Optimization
AI-powered Digital Twins, when combined with Smart Process Modeling, provide end-to-end visibility into the supply chain, allowing businesses to simulate, analyze, and optimize logistics, inventory, and procurement strategies.
How It Works:
- Digital twins create a real-time simulation of the entire supply chain, mapping and monitoring every stage from raw material procurement to product delivery.
- AI-driven Smart Process Modeling runs “what-if” scenarios to analyze potential disruptions, allowing businesses to proactively adjust their supply chain strategy.
- Predictive analytics and machine learning help optimize inventory levels, improving Just-In-Time (JIT) production without overstocking or material shortages.
- IoT-enabled Digital Twins provide real-time tracking of shipments, warehouse conditions, and demand fluctuations, ensuring operational agility.
Key Benefits:
✅ AI simulations anticipate demand shifts and disruptions.
✅ Digital twins monitor shipments and inventory in real time.
✅ AI optimizes routes, supplier collaboration, and fulfillment.
✅ Prevents overproduction, excess inventory, and inefficiencies.
5. Human-Robot Collaboration
AI-powered digital twins simulate interactions between human workers and robotic systems, enhancing workplace efficiency and safety.
How It Works:
- AI-driven simulations analyze ergonomic factors, movement patterns, and safety risks.
- Digital twins train autonomous robots to perform precise, repetitive tasks alongside human workers.
- AI-powered vision systems help robots detect, adapt, and respond to human actions.
Key Benefits:
✅ Increases automation without replacing human workers, optimizing hybrid workflows.
✅ Enhances workplace safety by predicting and preventing accidents.
✅ Boosts manufacturing efficiency by balancing robotic precision with human adaptability.
| Challenges & Considerations in Implementing AI & Digital Twins
Key Challenges & Solutions:
- Data Integration & Legacy System Compatibility – Deploy middleware and edge computing solutions.
- Cybersecurity Risks – Implement end-to-end encryption, Zero Trust security, and real-time monitoring.
- High Initial Investment Costs – Start with small-scale pilots and adopt cloud-based AI services.
- Scalability Issues – Develop modular AI architectures and optimize data processing.
- Skill Gap in AI & Digital Twins – Invest in AI upskilling and no-code AI tools.
WalkingTree Technologies enable manufacturers to transform their operational efficiency, predictive maintenance, and real-time process optimization. Our expertise lies in designing custom AI-driven Digital Twin frameworks, seamlessly integrating with Industrial IoT and cloud-based AI models for scalable, real-time simulation and monitoring.
Our AI & Digital Twin Expertise
WalkingTree Technologies delivers tailor-made AI-powered Digital Twin solutions that empower organizations across manufacturing, logistics, and industrial automation. Our expertise includes:
✅Custom AI-driven Digital Twin Frameworks
- We design bespoke digital twin solutions that replicate industrial assets, factory floors, and logistics ecosystems for real-time tracking and optimization.
- Our AI-driven models facilitate end-to-end operational visibility, enabling data-driven decision-making at every stage of production.
✅Cloud-based AI Models for Scalable, Real-Time Monitoring
- WalkingTree employs cloud-based Digital Twin architectures to provide scalable, multi-site monitoring solutions.
- Our AI-integrated models analyze vast amounts of real-time sensor data to enhance manufacturing productivity and predictive maintenance.
- By leveraging cloud computing and edge AI, we ensure fast, responsive insights without excessive infrastructure costs.
| Take the Next Step with WalkingTree
Are you ready to transform your manufacturing operations with AI-powered Digital Twins? Connect with WalkingTree Technologies today to explore how our cutting-edge solutions can enhance efficiency, reduce costs, and optimize production outcomes. Contact us now to schedule a consultation and take the first step towards smarter manufacturing.